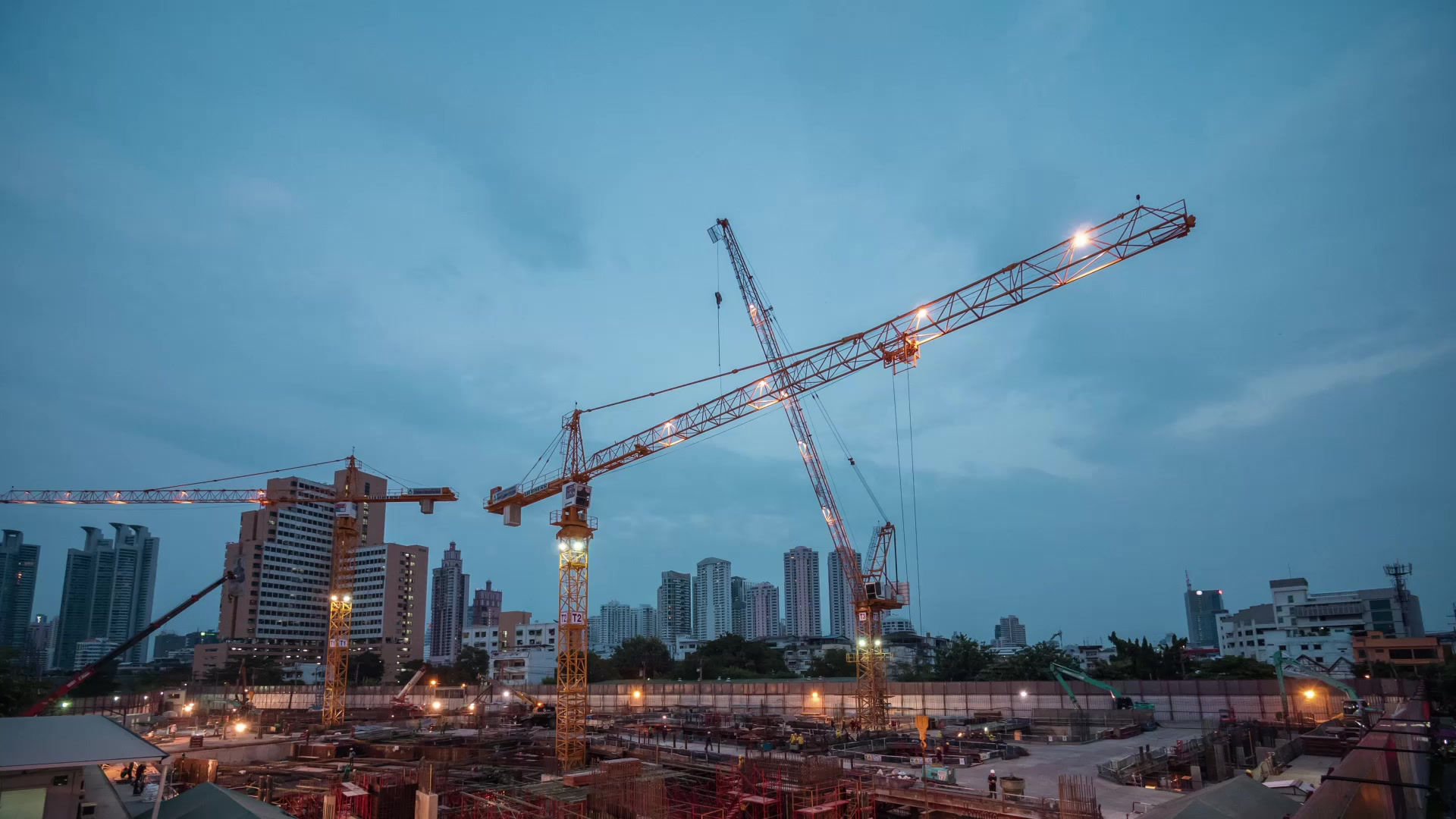
Solar Power
Solar feasibility studies are performed with the aid of computer modelled solar tracking software to determine maximum solar exposure analysis. Larger installations use 3D roof area drawings utilising laser scanning technology for mapping to aid the design and layout of the proposed solar array.
​
​
“How Do Solar Panels Work?
Solar panels are comprised of several individual solar cells which are composed of layers of silicon, phosphorus (which provides the negative charge) and boron (which provides the positive charge). Solar panels absorb the photons and initiate an electric current. The resulting energy generated from photos striking the surface of the solar panel allows electrons to be knocked out of their atomic orbits and released into the electric field generated by the solar cells which then pull these free electrons into a directional current This entire process is known as the photovoltaic effect.”, Page 3, The Solar Panel Pocket Guide, Ecogeneration, http://ecogeneration.com.au
​
​
“Module Types
There are various module types which are commercially available on the market today. The following is a non-exhaustive snapshot of commonly used modules.
60 Cell vs 72 Cell Module – standard 60 cell modules (referring to standard 6-inch cells) are most commonly used for residential and commercial installations. With dimensions of approximately 1.65m by 1m they are designed to have a sufficiently large collector area while still being easy to handle. 72 cell modules are most commonly used in large commercial, industrial and utility scale work. Through physically larger (approximately 1.95m by 1m) and more difficult to handle in the work environment (ground mount or large roof surfaces) and inherent reduction in balance-of-systems makes them an attractive option for larger jobs.
Mono v Poly – the difference between monocrystalline and poly or multicrystalline is the manufacturing process. Monocrystalline cells are formed by drawings up molten silicon starting from a seed crystal of uniform lattice structure silicon. As the silicon boule is drawn it cools with a lattice structure which follows the seed crystal. The single crystal boule is then cut into cells. Polycrystalline cells are usually formed by being pressed in a die or extruded. When this is done the lattice structure is not uniform, hence multicrystalline. Generally, monocrystalline cells are more efficient than multicrystalline cells.
​
N-Type vs P-Type – N-Type and P-Type refer to the type of bulk silicon used to make the cell. To set up an electric field which the cell, a P-N layer needs to be created. This is done by “doping” bulk silicon with elements such as boron for P-type and phosphorus for N-type. Most cells have P-type bulk layer for the historical reason that they perform better in extra-terrestrial applications. However, as the industry has evolved most PV applications are terrestrial, which is better suited to N-type bulk silicon. N-type bulk silicon cells usually have a price premium associated with them due to differences in the manufacturing process.
Half Cell – half cell modules are a relatively new type of module. These modules simply take advantage of reduced resistivity loss by halving the current from each cell. They are basically two parallel modules of series-connected cells put into a single encapsulation. Performance can be boosted by 5.8W per module. A drawback however may be that the leads for these modules are in the centre of the module.
Double Glass Modules – double glass modules use a standard cell type encapsulated with glass on both the front and the rear of the module (as opposed to the standard Tedlar backsheet). These modules offer superior strength and as they are frameless, they do not need to be earthed.
Bifacial Modules – these modules are also double glass modules, however they use a clear EVA (Ethylene-vinyl Acetate) and cells with a rear busbar instead of a rear conductor which covers the entirety of the cell. This allows light to not enter the cell from the front but also from the rear, thereby increasing its overall yield.”, Page 4-6, The Solar Panel Pocket Guide, Ecogeneration, http://ecogeneration.com.au
​
​
"Module Selection
Selecting a module can be a difficult supply chain decision. Most module manufacturers present a very similar value proposition and specification sheets provide little differentiation. The following list is meant to provide some guidance for selecting a specific manufacturer or specific module:
• what is the cost of the module?
• what is the performance and workmanship warranty of the module?
• is the warranty backed by a third party?
• is the warranty process simple and transparent?
• does the manufacturer perform electroluminescence testing on batch samples if not on every module?
• is the module PID Free?
• is the module tested for salt mist and ammonia corrosion?
• what is the power temperature coefficient (Pmax)?
• what is the front and back load capacity of the module?
• what is the trade history of the manufacturer?
• does the manufacturer have a diversified product line?
• does the manufacturer provide product support or value add services?
• does the manufacturer provide financing?
• does the manufacturer have a local presence?
”, Page 6, The Solar Panel Pocket Guide, Ecogeneration, http://ecogeneration.com.au
​
​
“Orientation
The importance of tilt angle and azimuth.
PV modules absorb solar radiation directly from the sun or from sunlight reflected off clouds or the area surrounding the module. Pointing the PV module at the sunlight will maximise the output performance. The PV module is most efficient when the sun’s rays are perpendicular to the module’s surface.
From your previous solar training or high school science classes, in the southern hemisphere, that is Australia, the sun is in the northern sky, it rises in the east and sets in the west and is higher in the sky in summer and lower in winter.
A dual tracking mounting system is the ultimate solution to follow the sun and get maximum output but this is not practical solution due to cost and engineering considerations. A fixed module will not always perform to its maximum efficiency but it is the easiest and cheapest option.
​
Azimuth:
Azimuth is the angle measured in a clockwise direction from north that the modules are facing. True north is the best option to point the PV modules but that is not always achievable owing to the fact that the builder built the roof you are mounting the modules on facing some other direction. In general, according to the CEC accreditation website (https://www.solaraccreditation.com.au/installers/compliance-and-standards/accreditation-guidelines.html) the difference on daily solar irradiation collection in Sydney between north, east & west is minimal in summer but substantial in winter (see table).
If a north facing array is not possible, then the argument continues whether an east or west facing array is better. With self-consumption being a major reason to install PV nowadays, consider when the customer will use the generated energy.
Solar collection efficiency compared to North (Sydney)
Tilt: 20 deg East West
Summer -2 % -1 %
Winter -42 % -43 %
​
For example, charging batteries to use at night… maybe east facing, using air-conditioning after a hot day… maybe west facing.
In the end, most designers/installers have little choice, the azimuth is decided where they can mount the whole array.
Tilt Angle:
As mentioned earlier the idea tilt angle for the PV module is perpendicular to the sun’s rays. PV modules should be tilted at an angle approximately equal to the site’s latitude. This will give the best average, taking into account the angle of the sun over the entire year.
For a grid-connected PV system on a domestic pitched roof, the roof pitch will be the resultant tilt angle. This is not ideal but the most practical and affordable. If using a tilt frame on a flat roof then aim for an angle closer to the site’s latitude.
For off-grid systems, the tilt angle is critical. In winter, when the sun is lower in the sky, it is paramount that the PV have a larger tilt angle to get the most out of the winter sun. Typically in off-grid systems, ground mount or tilt frame systems are used to get tilt angles of latitude plus 10-15 deg.
Shading:
PV modules generate electrical power based on the amount of sunlight hitting the module, then any reduction of sunlight caused by shading will reduce the output.
When shading strikes the module, the bypass diodes kick in and the output of the module can be reduced by the shaded cells. The worst case scenario for shading is when a line of shade crosses across all columns of the cells in the module and the output is reduced to zero.
The output of an array with PV modules, connected in series to a string inverter, can be reduced dramatically by the shaded module/s. So if shading is going to be a problem, then consider micros or optimisers. Both micro inverters and power optimisers essentially allow every solar panel in a system to operate independently, so that overall system energy production is not overly affected by just one or two shaded panels.
Amorphous silicon solar cells are said to be better at handling shading than crystalline silicon solar panels, but generally speaking the relatively low overall efficiency of amorphous panels means that crystalline modules are generally a better choice. Roughly half as efficient means that you need twice the roof space for mounting for the equivalent output. Not a practical solution with limited roof space.
Initial positioning of the array to minimise shading is important as is ongoing maintenance. Trees grow and need to be trimmed in order to maintain a shade-free array.”, Page 8-9, The Solar Panel Pocket Guide, Ecogeneration, http://ecogeneration.com.au
​
​
“The Weather Effect On Solar Modules
When you think about it, we place PV modules in the harshest conditions because they need sunlight to work. In hourly/daily changing weather conditions, hot one minute, cold the next, wet, frosty, you name it – most PV modules just keep on generating. Nowadays high quality PV modules are very durable.
Temperature:
The sun is shining, the temperature is rising, the PV modules are in full sun, generating heaps of energy…right? Well, not quite! As the ambient temperature rises, the performance of the PV module reduces. This is just a fact of silicon PV modules.
As the PV modules heat up, the Isc increases slightly but the Voc drops more. Using the formula P = V*I, the larger drop of Voc causes the power to decrease.
Conversely, at low ambient temperature, the performance of PV modules increases, as the Voc increases, (the Isc decreases slightly). This is why you use the lowest temperature of the location to calculate the maximum Voc.
So the ideal location for PV modules is clear, sunny days, with low ambient temperatures like alpine areas of Germany.
Cloud:
Put simply, PV modules need sunlight to perform. More sun equals more generation. Cloud reduces the amount of sunlight reaching the PV modules so generation reduces accordingly.
Rain:
With rain comes clouds, so expect a reduction of performance. However, rain can be good for PV modules as well. Over time PV modules can accumulate dust, dirt and bird droppings which reduce overall performance. A good rain shower will clean the PV modules returning them to a better output.
It is important that PV modules are mounted at least 10 deg tilt so the water will run off. Pooling of water on the surface of the PV module may cause damage in the long term.
Wind:
Wind may have a positive effect on PV module performance. The cooling effect of wind will keep the ambient temperature down so performance increases.
Wind however, can cause problems, if the PV modules are not mounted correctly on the roof. PV modules mounted too close to the edges or overhanging the ridge line are subjected to increased wind load which may physically damage the PV modules.
Hail:
Hail storms may damage the glass surface of the PV module. PV module are designed to withstand hail; typically quality PV modules can withstand 25mm-diameter hail at 23 m/s.
PV modules with hail damage (a damaged glass surface) may still work but will degrade the overall performance of the array if a string inverter is used. Eventually, water will impregnate the damaged surface and cause total module failure.
Lightning:
Stating the obvious, a direct lighting strike on your PV array will cause extensive damage. In lightning prone areas consider using a direct strike lightning protection like they do in Germany. If using ground mount arrays and underground cable runs surge protection should be installed on each end to protect the PV modules as well as the inverter and equipment.
Snow:
Snow on the face of PV modules acts similarly to shading. Using micro or optimisers instead of a string inverter may increase the overall performance of the array. The weight of the snow adds to the static weight of the array on the mounting system and the roof structure needs to be taken into account when designing the system.
Salt Water Spray:
In coastal areas, sea spray (high salt concentration in the air) will influence the performance of PV modules. Sea spray will get in everywhere so select a PV module suitable for the intended environment. More regular cleaning will also maintain the output and longevity of the PV array.”, Page 9-10, The Solar Panel Pocket Guide, Ecogeneration, http://ecogeneration.com.au
​Inverters
“Hybrid
The PV array is directly connected to the hybrid inverter as well as the grid. The hybrid inverter will charge the battery storage and converts the dc current from the battery storage into ac current for the attached loads. Hybrid inverters do not supple ac current when the grid is disconnected.”, Page 4, The Inverter Pocket Guide, Ecogeneration, http://ecogeneration.com.au
“What is Multi-Mode Inverter?
A multi-mode inverter is an inverter which operates in more than one mode, that is it operates from the grid when available and off-grid mode when the grid is disconnected. A multimode inverter requires battery storage to be connected to operate in the off-grid mode.”, Page 4, The Inverter Pocket Guide, Ecogeneration, http://ecogeneration.com.au
“Common Mistakes When Installing Inverters
• Voltage rise: Too small cable between inverter and switchboard,
• PV module voltages and current not marched to attached inverter,
• Inverter clipping caused by connecting too many inverters in a string,
• Too many micro on a branch,
• Not following manufacturer’s instructions, especially in relation to clearances and ventilation,
• Location – not installing in direct sunlight/weather. Check the IP rating,
• When mounting an inverter, think switchboard and apply the same mounting conditions (AS/NZS 3000).”, Page 10, The Inverter Pocket Guide, Ecogeneration, http://ecogeneration.com.au
​
“Replacing A Faulty Inverter
• Replace like for like if the inverter is still available,
• If no longer available, replace with the equivalent inverter as recommended by the original manufacturer,
• Select an equivalent inverter, matching the power, voltage, current and whether it is transformer/transformerless technology. You may be required to upgrade the whole system to current Standards & CEC guidelines so check with your local electricity regulator. It may be better and cheaper to scrap the old system and install a whole new system.
Remember to isolate, test and lock before removing and replacing the inverter or working on the system.”, Page 10, The Inverter Pocket Guide, Ecogeneration, http://ecogeneration.com.au